A small metallic particle that had contaminated a product line was brought to SI’s Materials…
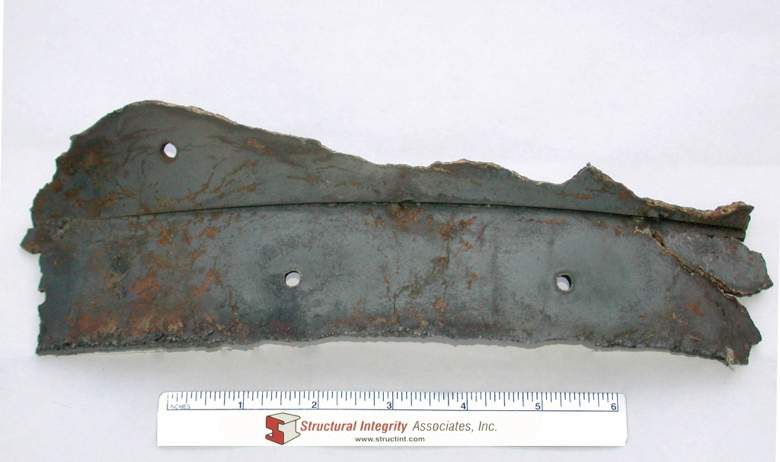
Polythionic SCC
By: Wendy Weiss
Structural Integrity Associates, Inc. (SI) was asked to examine a section of a burner gas ring from a boiler located at a chemical plant (Figure 1) and determine the cause of the corrosion and cracking. The approximately 10-year old burner ring was manufactured with Type 304 austenitic stainless steel. Reportedly, the corroded side of the burner ring was exposed to flue gas and the other side was exposed to methane gas. The outlet flue gas temperature was reported to be between 250 and 300°F.
Figure 1. The OD surface of the burner ring sample showing corrosion and cracking.
Cross-sectional samples were cut through the cracking, mounted and prepared for evaluation of the damage morphology. The damage consisted of intergranular attack and oxidation, intergranular (around grain) cracking and grain “fall out”. (Figures 2 and 3). In addition to the intergranular cracking, a few areas with transgranular (through grain) cracking were also observed (Figure 4).
Figure 2. Image from a through-wall crack
showing intergranular attack and grain
fallout. (original magnification: 100X
Figure 3. Images showing the intergranular
attack and oxide-lined grain boundaries,
as well as areas of grain fallout. (original
magnification: 200X and 400X)
Figure 4. Area of transgranular
cracking. (original magnification: 400X)
We removed another cross-section from the burner ring and prepared for examination in a scanning electron microscope (SEM) so that the crack deposits could be analyzed using energy dispersive X-ray spectroscopy (EDS) to identify the elements present. Various cracks in the sample were analyzed and the deposits in all areas were similar. All of the areas analyzed contained iron, chromium, nickel and silicon from the base metal as well as significant amounts of oxygen, indicating oxides were present, and a moderate amount of sulfur (Figure 5). Additionally, chlorine was present in a few areas, but it was not widespread.
The intergranular attack, intergranular cracking and grain fall out are all characteristics of stress corrosion cracking due to polythionic acid in sensitized austenitic stainless steels. This type of stress corrosion cracking occurs when sulfur-containing deposits mix with oxygen and moisture to form polythionic acids of the type H2SxOy. In this case, sulfur in the deposits from the flue gas was plentiful. Polythionic acid SCC requires the presence of moisture, and therefore occurs during downtime or at dew point temperatures when moisture can form during operation.
Sensitization, which is the condition when chromium carbides form on the grain boundaries resulting in a chromium-depleted region immediately adjacent to the grain boundaries, of Type 304 stainless steel normally occurs at temperatures between 750 and 1500°F (400 – 815°C). The transgranular cracking, which is indicative of chloride-induced SCC, which was observed in the sample, was less abundant than the intergranular cracking and in some cases the transgranular cracking was emanating from the intergranular corrosion, suggesting the polythionic acid attack had occurred first. Though it is not possible to determine if the chloride SCC was secondary to the polythionic acid attack, it is clear that the polythionic acid attack is the major damage mechanism.
Because the burner gas ring reportedly operates at temperatures in the 250 to 300°F range, the component was not sensitized during normal operation unless the metal temperature is substantially higher than the gas temperature. Because the damage in the burner ring section was not localized to the weld, the sensitization cannot be attributed to welding. It is possible that the material was heat-treated improperly and has been in the sensitized condition since construction. Another, more likely possibility is that the sensitization occurred during operation, perhaps during upset conditions when the burner gas ring metal condition could have been above 750°F.
Ensuring that the Type 304 stainless steel burner gas ring is not exposed to temperatures that can cause sensitization will help mitigate the polythionic acid attack, as it only occurs in sensitized material. Chloride-induced SCC can occur in Type 304 stainless steel whether it is sensitized or not. Keeping the burner gas ring dry and as free from deposits as possible will help prevent both the polythionic acid and chloride SCC from recurring.