A small metallic particle that had contaminated a product line was brought to SI’s Materials…
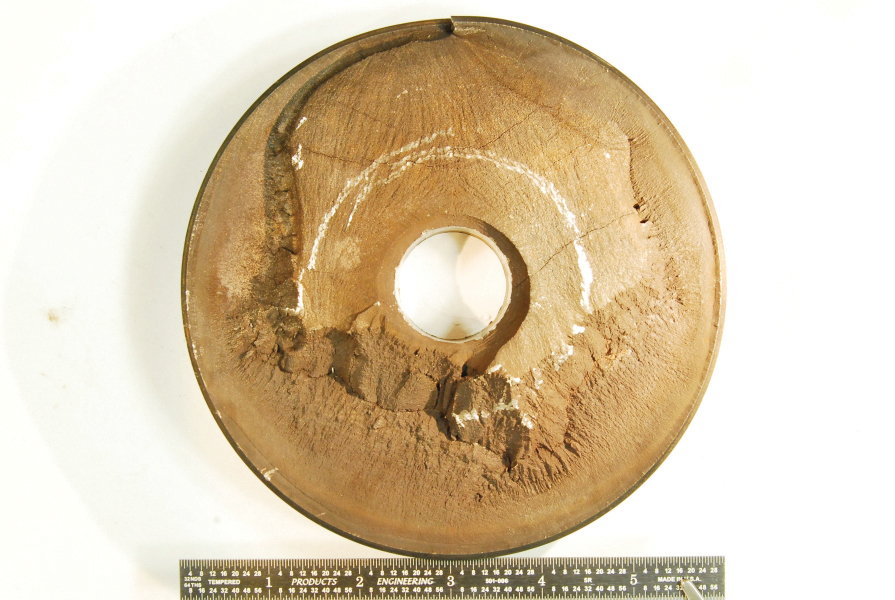
Stress Accelerated Grain Boundary Oxidation (SAGBO) in Nickel Alloys
By: Amanda Robinson, Tony Studer
Modern nickel-iron superalloys have enabled certain high pressure components, such as gas turbine blades, turbine studs, springs, and nozzles to operate at higher temperatures. Many of these superalloys have been found to suffer from a unique damage mechanism called stress accelerated grain boundary oxidation (SAGBO) cracking. SAGBO is a subclass of stress corrosion cracking that is caused by the synergistic effect of tensile stress (either residual or applied), temperature, and the presence of oxygen. SAGBO occurs when oxygen diffuses along the grain boundaries and through either embrittlement or oxide wedging, the grain boundaries separate.
THE TWO (2) PROPOSED MECHANISMS MOST OFTEN DISCUSSED IN THE LITERATURE ARE:
Oxidation Precedes Crack Growth: Oxide is formed at a crack tip and preferentially continues along the grain boundary. The wedge shaped oxide forces the grain boundary apart. Oxygen diffuses down the new crack tip and the process repeats.
Embrittlement Precedes Crack Growth: Oxygen diffuses into the grain boundary and causes embrittlement, possibly by brittle phase formation, solute segregation, or removal of strengthening precipitates. As the grain boundary weakens, the local tensile stresses cause the grain boundary to open. Oxygen then diffuses at the front of the new crack tip.
Typical characteristics of SAGBO are preferential oxide formations along grain boundaries, intergranular oxide-filled cracks, and the presence of an “oxygen getter” along the grain boundaries. The literature has proposed that niobium oxide can form on the grain boundaries ahead of the crack tip, which leads to the brittle intergranular fracture. SAGBO usually occurs at a temperature range of one-third to one-half the material’s melting temperature.
CASE STUDY 1
Structural Integrity received a fractured Alloy 718 stud from the high pressure section of the inner casing of a steam turbine. During normal operation, the area is exposed to dry steam (approximately 800°F at 800 psia). Discussions with plant personnel indicated that:
- The stud had been exposed to higher temperatures due to a gland packing failure.
- The temperature and pressure inside the inner shell that these studs hold together is approximately 1,000°F and 3,500 psig.
- The stud was in service for approximately 1.5 years before it failed.
The fracture surface was examined using a stereoscope to evaluate the fractographic features. The surface was rough and irregular and several secondary cracks were observed (Figure 1). Based on the visual examination, the origin of the fracture and the fracture path were identified.
Figure 1: Fractured Alloy 718 Stud
Two cross-sectional samples were removed through the fracture for metallographic examination. At high magnifications it was evident that the fracture and secondary cracks were primarily intergranular (around grain), with a few transgranular (through grain) branches (Figure 2). Additionally, several apparently disconnected cracks were observed. All of the secondary cracks were lined with oxide (Figure 3). No creep damage, such as voids or microcracks, was observed. The oxide-lined intergranular cracks with a brittle appearance are characteristic of SAGBO in Alloy 718.
Figure 2: Fracture Surface
We examined both the fracture surface and one of the cross-sectional samples in a scanning electron microscope (SEM). The SEM analysis of the fracture confirmed the primarily intergranular surface appearance, with significant branches. Figure 4 shows a high magnification image of the secondary branches. Several of the transgranular branches appeared to be propagating along twinned grains within the austenite matrix. Energy dispersive X-ray spectroscopy (EDS) analysis of the cracks revealed oxygen and niobium within the grain boundaries. No corrosive contaminants were identified. Niobium was also observed along the microstructural twinning within the matrix. The presence of niobium along the twinning and grain boundaries results in a microstructure susceptible to SAGBO, because a grain boundary phase acts to enhance oxygen diffusion. Tensile and chemistry tests met the specifications for Alloy 718.
Figure 3: Secondary Cracks
The stud failure mechanism was confirmed to be SAGBO. The turbine stud exhibited extensive oxide-filled intergranular branched cracking with niobium present along the grain boundaries.
Figure 4: SEM Image of Crack
CASE STUDY 2
Structural Integrity received a desuperheat nozzle from a main steam attemperator that contained a failed Nimonic 90 spring. It was in service less than one year, where it was believed to have experienced temperatures between the normal steam temperature (1075°F) and the water temperature (330°F). A concern was that the nozzle was getting stuck open and the spindle was not fully reseated once there was no water pressure. If this occurred, the spring could have experienced a quick temperature change of about 700°F, leading to thermal shock.
One of the fracture surfaces was removed from the spring for further evaluation (Figure 5). The fracture surface was examined in an SEM including in situ EDS analysis. Aside from the elements in Nimonic 90, only oxygen was detected on the fracture surface. Following the EDS analysis, the fracture surface was ultrasonically cleaned and re-examined in the SEM. The fracture surface was relatively rough and irregular and exhibited secondary cracks that appeared to be intergranular.
Figure 5: Fractured Nimonic 90 Spring
Following the SEM examination, a cross-section through the fracture surface was prepared for metallographic examination. The metal along the surface of the spring exhibited minor preferential grain boundary oxidation. A secondary crack that was observed adjacent to the primary fracture exhibited branching with extensive branching at the tip (Figure 6). The crack was oxide-filled with a light phase in the center of the oxide. The metallographic sample was examined in the SEM for evaluation of the oxide layers within the secondary crack, and in particular, the light phase in the center of the crack (Figure 7). EDS analysis revealed that the light phase along the center of the crack was rich in nickel.
Figure 6: Secondary Crack Adjacent to the Primary Fracture
The failure of the nozzle spring was attributed to SAGBO based on the general appearance of the secondary intergranular crack in the spring with the Ni-rich filament. The failure was consistent with the nozzle having stuck open after the valve was closed, which can reportedly expose the spring to steam temperatures up to 1075°F, putting it in a temperature range in which it is susceptible to SAGBO.
Figure 7: SEM Image of Secondary Crack
RECOMMENDATIONS
Are there nickel-iron superalloys in your facility that could be experiencing SAGBO damage? Over the past several years, Structural Integrity has identified SAGBO failures in numerous different components (turbine studs, springs, and nozzles) fabricated from three different materials (Alloy 718, Inco 901, Nimonic 90). However, nickel-iron superalloys operating in high temperature oxygenated environments are susceptible. Since SAGBO failures typically initiate at the surface exposed to oxygen, nondestructive techniques such as Penetrant Testing (PT) are helpful for identifying damage.
There are several methods to reduce or mitigate the formation of SAGBO, which include reducing the applied tensile stress, decreasing the oxygen partial pressure, modifying chemical composition (by initiating a material change), modifying microstructure (through heat treating), modifying thermomechanical processing, and the application of an oxidation resistant coating. Any changes to the system should be reviewed with the OEM to determine the potential effect on other system components and overall system performance.