A small metallic particle that had contaminated a product line was brought to SI’s Materials…
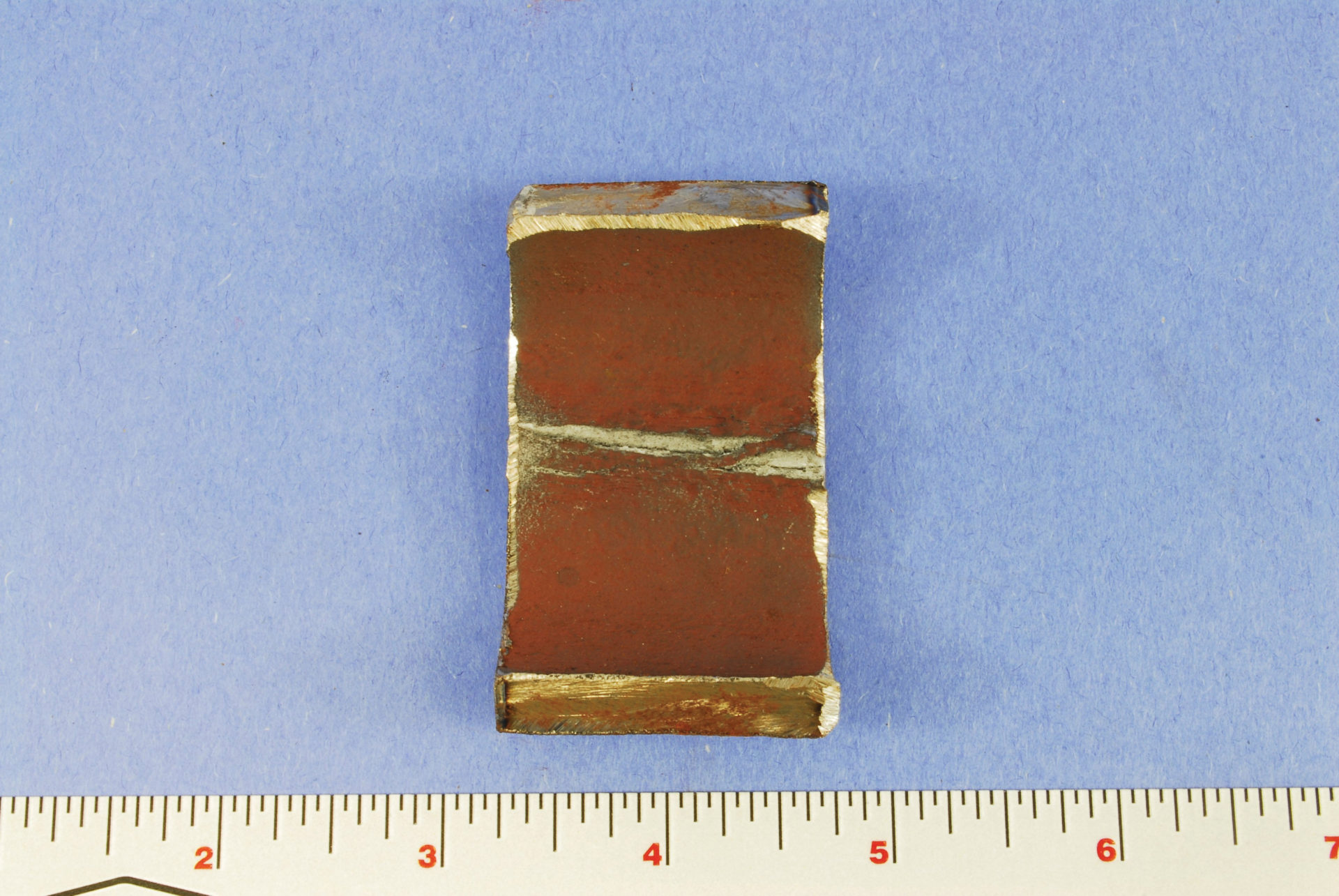
Unusual Hydrogen Damage Failure
By: Wendy Weiss, Tony Studer, P.E.
While hydrogen damage is most often associated with severe gouging on the internal surface of a tube, it can occur in the absence of gouging. Structural Integrity received four waterwall tube sections from a coal fired unit. An Ultrasonic (UT) inspection had detected hydrogen damage ranging from moderate to severe. The table below summarizes the identification, location, and damage level detected based on the UT inspection for the tubes received.
We are asked to examine the front waterwall deflection and rear nose arch tubes for hydrogen damage and to assess the extent of the damage.
A ring section was cut through regions identified as containing hydrogen damage from each tube section (Tubes 5, 7, 8, and 83) and prepared for metallographic examination. The prepared rings were examined using a metallurgical microscope and no obvious hydrogen damage was observed. In order to provide better edge retention and increased sensitivity, smaller sections were removed from the hot sides of Tubes 5, 7, and 8, mounted, and prepared for metallographic examination. Upon closer examination, possible hydrogen damage was observed in all three tubes. Figure 1 shows the typical appearance of the hydrogen damage observed in Tubes 5, 7, and 8. The hydrogen damage consisted of partial separation of the ferrite grain boundaries (fissures).
A sample was removed from the hot side of Tube 83 and flattened, which opened up a crack on the internal surface (Figure 2). The crack was not associated with gouging. After the sample was flattened, it was cross-sectioned, mounted and prepared for metallographic examination. Figure 3 shows the grain boundary fissuring, which became much more evident because the flattening caused the fissures to open. The hydrogen damage had penetrated about half way through wall.
The internal deposit loading was measured on Tubes 7, 8, and 83 and the results are provided in the table below. The heaviest deposit loading value was associated with the most severe hydrogen damage based on the inspection results.
The waterwall tubes contained irreversible hydrogen damage. No severe ID wastage was observed on these tubes. This agrees with the ultrasonic inspection, which did not detect any significant wall thinning associated with the hydrogen damage detected on the deflection and nose arch tubes. The appearance of the hydrogen damage was not typical. The damage consisted of discrete grain boundary fissures, which were not readily discernible. A major factor contributing to the hydrogen damage in the deflection and rear arch tubes is the heavy internal deposit buildup. The heavy deposits would have shielded the corrosion sites so that the hydrogen atoms formed during the corrosion process were not washed away, perhaps allowing the hydrogen damage to occur rapidly and before significant gouging occurred. The heavy deposits would also act as a thermal barrier, which increases the metal interface temperature. The increased metal interface temperature may have resulted in increased corrosion rate, similarly allowing the hydrogen damage to form before significant gouging occurred.
We recommended replacing all severe and moderate-severe damaged tubes and then performing a chemical clean of the unit to remove the very heavy deposit buildup and help eliminate the continued formation of hydrogen damage in the unit.